For centuries, metal casting has been a cornerstone of craftsmanship. Ancient civilizations developed the technique to create intricate and beautiful works of art from bronze, copper, silver, and other metals.
Nowadays, this ancient practice is being revived by modern artisans who are using it to create stunning pieces that combine traditional craft with new-age creativity. Through fire and molten metal, these skilled craftsmen are redefining the boundaries of what can be created through metal forging.
Join us as we explore how crafting in fire is bringing an age-old tradition back into the spotlight.
Introduction to Metal Casting

Metal Casting is an ancient and timeless art form that has been used in many cultures around the world for centuries. It involves taking molten metal from a furnace or kiln and pouring it into a mold to create intricate shapes and objects.
The process of Metal Casting requires attention to detail, skillful manipulation of materials, and sheer patience – but the results can be stunningly beautiful pieces with unique character. With modern technology, craftspeople can create some truly remarkable works of art through this traditional technique.
In this article, we will take a deeper look at what metal casting is, its origins, and why it remains popular today. Well also explore how different types of metals affect the final product as well as go over safety precautions when working with hot metals.
By the end, you should have a better understanding of how crafting in a fire can produce amazing artwork!
In the field of industrial safety and infrastructure protection, implementing advanced solutions like a fire wall is essential for safeguarding equipment and facilities. Modern fire barriers are designed to offer robust protection against potential hazards, including transformer explosions. Integrating effective fire walls can significantly enhance safety and prevent costly damage in high-risk environments.
Tools and Materials for Metal Casting

Metal casting is an ancient process of crafting that has been revived and modernized in recent times. The tools and materials necessary for metal casting range from simple items like an open-hearth furnace, a crucible, or even a kitchen oven to more complex pieces of equipment like wax injection machines or vacuum chambers.
A variety of metals can be used in the process, such as bronze, brass, aluminum, copper alloys, and steel. Additionally, molds are needed which can be made from plaster casts or special sand molds that will contain the molten metal until it cools down and solidifies into the desired shape.
Complete this intricate craftsmanship requires additional materials like fluxes to improve metal flow during pouring; heat insulators; safety gear such as face shields or protective clothing; refining agents for smelting impurities away before pouring; sprays for mold release when opening up parts after cooling; polishing cloths for finishing touches on castings made out of precious metals. With the right knowledge and dedication, anyone with access to these tools and materials can take part in this rewarding activity that goes back centuries ago!
Basic Steps of Metal Casting
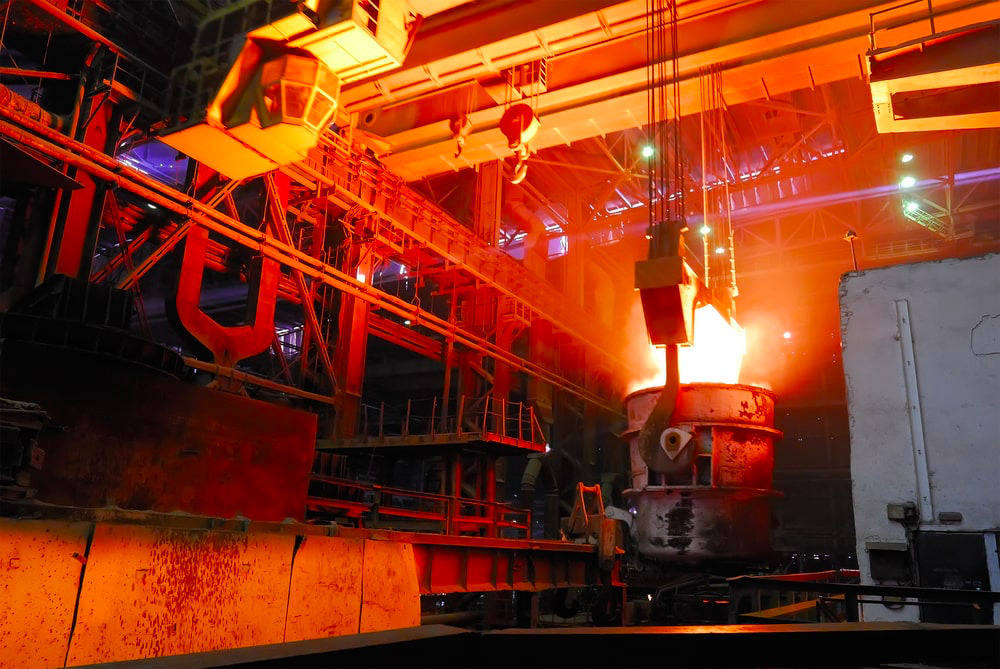
Metal casting is a process that dates back to ancient times and has been revived in recent years as an art form. It involves shaping metal into intricate shapes and designs by pouring molten metal into molds or casts.
The basic steps of the process involve:
- Preparing the mold – This requires creating a two-part mold from materials such as sand, plaster, or even wax, which will contain the shape of your desired object when it cools down.
- Melting the metal – Using furnaces and other tools, you must heat your chosen metals until they reach their melting point before pouring them into the prepared mold.
- Pouring the molten metal – Once at its proper temperature, take extreme caution when pouring it over your pre-made shape or design to avoid spilling any liquid onto yourself or nearby objects while also ensuring that all details are accounted for within your casted item’s design.
- Cooling/Removing – Allow enough time for everything to cool off before attempting to remove it from its container; this could take anywhere between 15 minutes for smaller items to several hours for bigger ones depending on what kind of material was used in the preparation of both pieces making up your mold box componentry
- Finishing/Polishing – After removal from its container use special abrasive tools to smooth out any imperfections on surface areas along with adding texture if desired while taking care not to damage fragile components present on parts whose geometry includes those elements
Conclusion
The Ancient Technique of Metal Casting Revived is a remarkable article that has highlighted the revival of an ancient technique. It demonstrates how metal casting has been used for centuries and still serves as an incredibly useful and valuable method today.
This article also discussed the materials needed to make a cast, including clay, sand, wax, and molten metal such as bronze or brass. Additionally, it outlined the process of creating casts step-by-step with clear examples.
All in all, this article provided readers with insight into both the history and modern use cases for metal casting. Click here to learn more about this fascinating ancient craft!