ERW pipes are an integral part of the manufacturing process in many industries. From water supply and drainage systems to structural support for buildings, these pipes have been a staple of construction for decades.
In this article, we will discuss the advantages that ERW pipes bring as well as their manufacturing process. We will explore how they can improve efficiency and reduce costs while providing superior durability when compared to other materials used in construction.
Additionally, we take a look at some of the safety considerations involved with using ERW pipes during installation and maintenance as well as their environmental impact. With all this information you will be better equipped to make informed decisions about your projects involving ERW piping.
Overview of Electric Resistance Welded (ERW) Pipes
Electric Resistance Welded (ERW) pipes are an integral part of many manufacturing processes. These high-quality components are used in a wide array of applications, from automotive to aerospace.
ERW pipes offer several advantages over other types of pipe, including increased strength and durability, uniformity in size, and cost savings. This article provides an overview of the benefits associated with ERW pipes as well as the process for their manufacture.
The electric resistance welding (ERW) process involves the use of heat to join metal pieces together via electrical current passing through them at extreme temperatures. During this process, pressure is applied along with heat so that the metal pieces can be welded into one continuous piece without any seams or weak points present in the joint area.
The resulting product is a strong and uniform ERW pipe made up of either carbon steel or stainless steel material – depending on its intended application – that has been tested for quality assurance purposes before being shipped out for installation or assembly within a project space. The main advantage associated with using ERW pipes over traditional methods such as soldering and brazing is that it allows manufacturers to produce higher quality parts faster while also reducing costs by eliminating manual labor requirements that would otherwise need to be undertaken during these more primitive operations.
Additionally, their superior strength attributes when compared against other forms of piping, make them ideal for use within demanding industries such as construction or oil & gas where environmental conditions may put extra strain on components used in projects across these sectors. In conclusion, Electric Resistance Welded (ERW) Pipes provide numerous advantages when compared to traditional methods; namely increased strength & durability alongside greater efficiency due to less manpower required throughout production cycles whilst still ensuring optimal levels of quality control remain constant throughout each batch produced thus making them suitable products for almost every industry imaginable today!
Advantages of ERW Pipes

ERW pipes offer a wide range of advantages that make them an attractive choice for use in many applications. The primary advantage is their cost efficiency, as they are cheaper to produce than other types of pipe.
ERW pipes require less labor and machinery during the manufacturing process, saving time and resources. They can also be used with a variety of materials, including carbon steel, stainless steel, aluminum, copper, and PVC. Furthermore, ERW pipes have a higher strength-to-weight ratio when compared with seamless or welded pipes due to their thinner walls which make them lighter yet still strong enough for most uses.
Additionally, these thin walls allow them to transport more material over long distances at high pressures without sacrificing performance or safety standards. Finally, ERW pipes are highly resistant to corrosion which makes them ideal for outdoor applications where exposure to weather elements would normally cause premature degradation in other types of piping systems.
Manufacturing Process for ERW Pipes
The manufacturing process for Electric Resistance Welding (ERW) pipes involves two main steps, cold forming and high-frequency welding. Cold forming is a procedure in which the steel material is formed into the desired shape and size by using rollers to stretch it through an open die.
This works well for creating long, straight sections of pipe without any bends or curves. High-frequency welding then follows this step to join all of the pieces together.
During this step, electric current passes between electrodes on both sides of the joint at a very high frequency causing localized heating that melts part of each side joining them together making a strong welded seam. After completion of these two steps, other processes may be necessary such as hydrostatic testing and finishing operations like threading or coating depending on what type of pipe you are looking to make.
Overall, electric resistance welding pipes offer great durability with minimal effort due to their simple yet effective manufacturing process.
Conclusion
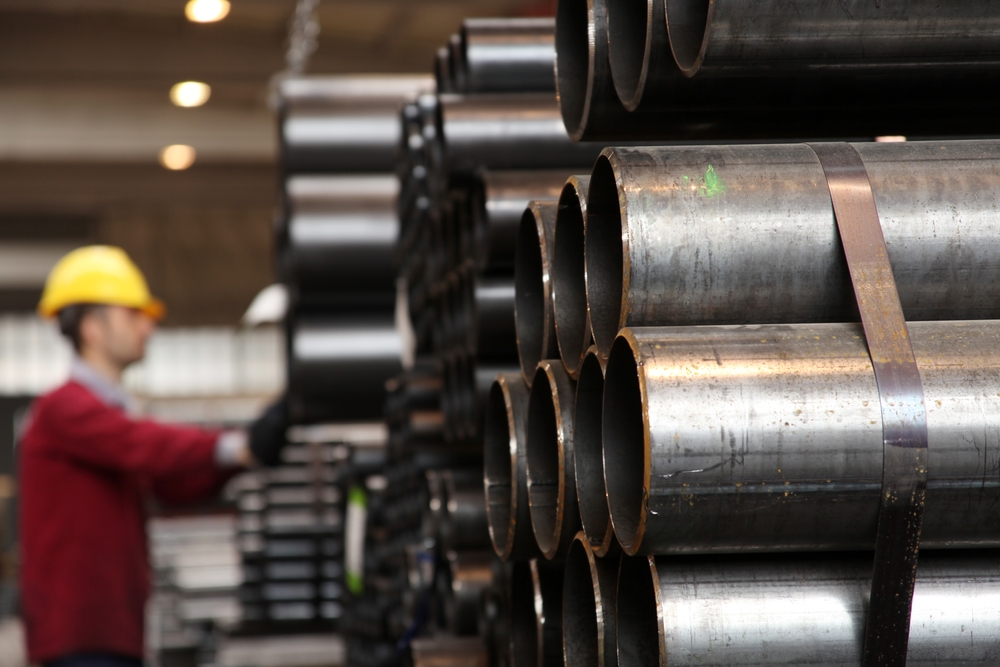
In conclusion, ERW pipe is highly advantageous due to its efficient manufacturing process and cost-effectiveness. Not only are they easy to manufacture, but the end product is a reliable and durable pipe that can be used in many applications.
By understanding the advantages of ERW pipes and the various steps of its manufacturing process, it’s possible to make an informed decision when selecting piping material for a project. With the right knowledge, ERW pipes may just be your best choice!